We use cookies to give you the best possible experience. To accept cookies continue browsing, or view our Cookies Policy to find out more.
The Ultimate Guide To Cotton Fabric Manufacturing: Part 3 - The Spinning Process
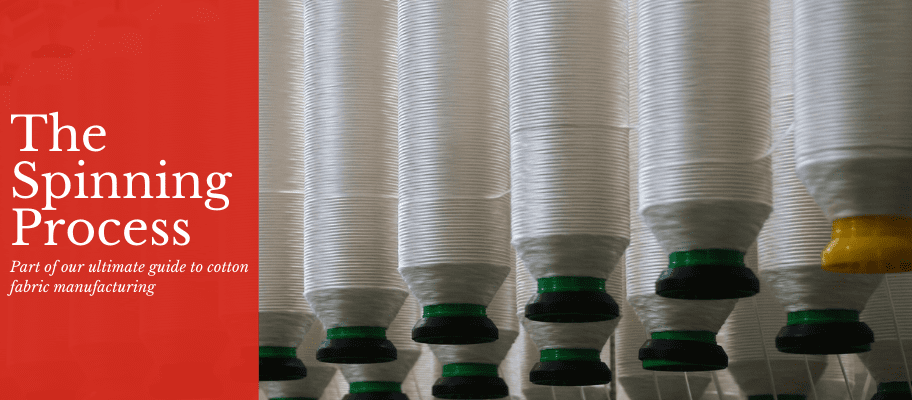
Now that the cotton has completed the carding and optional combing stage, it’s time to proceed to create the yarn through spinning.
There are a few different ways that you can spin yarn, but the most common ways of spinning as far as bed linen and towels are concerned are open-end spinning, ring spinning, or compact spinning. In this article we’ll go into detail on each spinning type, beginning with open-end spinning.
Open-end Spinning
Open-end spinning, also known as break spinning or rotor spinning, is a technology that was creating to allow creation of a yarn without the use of a spindle. The simplest way to describe this process is if you opened the door of a spin dryer full of sheets when it was still turning and pulled out 2 sheets, they would spin together as you pulled them out. The sliver from the carding process goes into the rotor where the rotor action twists around to spin the sliver into yarn that is continually drawn out of the chamber and wrapped into a bobbin.
While open-end spinning is the fastest and cheapest way of producing yarn – with it being up to five times faster than ring spinning - it does have its limitations. Open-end spinning is limited to the production of thicker or coarser yarns. The yarns are hairier, and the fabric will be more likely to pill or bobble, so it’s not a good method for making fine quality bed linen. As such, it’s generally better for making heavier fabrics such as towel.
Ring Spinning
The oldest system and based on original yarn spinning methods. Ring spinning is a continuous process in which the fibres are twisted and narrowed to create a fine rope of cotton fibres. The more the fibre is twisted, the softer the fabric will be. It works by using a ring frame made from pressed steel. Spindles sit on each side of the frame, while draughting rollers sit above them with a creel laded with bobbins of what's known as roving (an unspun thread).
The roving passes downwards from the bobbins to the draughting rollers, which are usually made up of three rollers. After draughting, the roving passes through a thread guide that is centred above the spindle. Here it is threaded through a small D ring known as a traveller. This is where the system gets its name from, as the traveller moves along the ring and the thread is attached to the existing thread on the spindle. Working together, the spindle and the traveller winds up the thread on the spindle and twists it into a yarn, guiding the thread onto the bobbin. The full bobbins are down wound onto a cone or cheese, creating a larger collection that can then be used for weaving.
Ring spinning isn't used in production as much as open-end systems, but it still produces a yarn quality that is of better quality than open end. It has the widest possible yarn count range and, as such, excels in creating very fine counts, making it ideal for luxury bedding. These fine yarns are smoother, more durable and much less hairy than an open-end yarn. However, due to the additional steps that go into the roving and winding of the yarn and the slower production rate, it results in it being much more expensive to produce the yarn by this method.
Compact Spinning
Compact spinning is a modern method that involves condensing the fibres together by air suction to create a more optimal integration into the yarn body. The air suction pulls the fibres into the yarn to give it smoothness and strength. The yarn is then tightly twisted. Because the fibres are sucked tightly into the yarn, good quality yarns can be produced from shorter staple length cotton as no fibres ended up sticking out. Another benefit is that the yarn can be produced with a higher speed than ring spinning.
While compact yarn is the least hairy of the methods presented here and will give a nice smooth fabric that makes it ideal for bed linen, it's still not as effective as combing the fibre before the spinning process as the shorter fibres are still there if it hasn't been combed first. Below you can see a comparison between the types of spinning we've talked about here.
What Are Yarn Counts?
Each yarn includes a yarn count number, which refers to the thickness or fineness of a yarn. Yarn counts are based on the ratio of weight to length in a yarn and are calculated through one of two count systems - direct and indirect.
In a direct yarn count system, you're measuring how much a given length of yarn weights, where the length of the yarn is fixed, and the weight is variable. Two units of measurements here are tex and denier. Tex refers to the number of grams per 1000 metres whereas denier refers to the number of grams per 9000 metres.
In an indirect yarn count system, you're trying to find out what length of yarn you would have in a given weight, so it's the weight that is fixed and the length that is variable. This is more often used but it's actually the more complicated of the two systems. Here the cotton count (or English cotton count) is the most common unit of measurement. To get to the cotton count you need to count how many 840-yard hanks (a measurement of the length per unit mass of yarn, 840 yards of cotton yarn is equal to one hank) make up one pound in weight. The number of hanks it takes is the cotton count. For example, a cotton count of 40 means that it takes 40 of the 840-yard hanks to make up a pound in weight. It's an upside-down system, because the lower the yarn count number, the thicker and heavier the yarn as it takes less hanks to make up a pound.
What Is A Yarn Ply?
The ply of a yarn refers to the number of single yarns that are used in making the final yarn. The most common ply is two-ply, which means that two yarns are twisted together to make a single yarn.
Two-ply yarns are stronger and give a more durable fabric than single ply yarns. These are often used in the ground warp for towels, and also used for the pile on towels toi give a smooth appearance and help resist flattening of the pile because they are more rigid.
You'll find two-ply yarns most often on bath mats or where a towel has a design as the two-ply yarns stay upright and give a clearer definition of the pattern on the bath mat.
The next step in the cotton fabric manufacturing process is weaving, which you can read about by clicking here.
The full guide:
Read Part One - The Harvesting and Cleaning Process
Read Part Two - The Carding and Combing Process
Read Part Three - The Spinning Process
Read Part Four - The Weaving Process
Read Part Five - The Finishing Process
Read Part Six - The Product Makeup Process For Bedding & Towels