We use cookies to give you the best possible experience. To accept cookies continue browsing, or view our Cookies Policy to find out more.
The Ultimate Guide To Cotton Fabric Manufacturing: Part 2 - Carding & Combing The Cotton
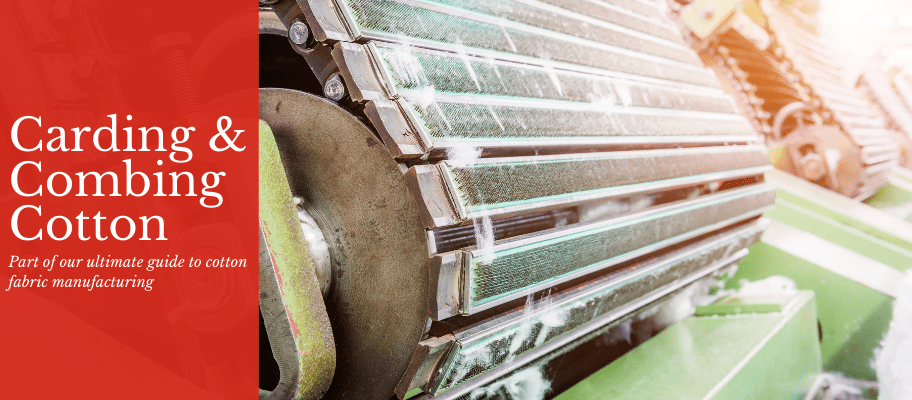
Welcome to the second part of our ultimate guide to cotton fabric manufacturing! In our first part (which you can read by clicking here) we went into detail and the harvesting and cleaning process of cotton before it is turned into yarn. In this post we’ll delve into the process of how cotton fabric is turned into yarn, so let’s get started!
We’ll begin by talking about the carding process, which is the first stage after the opening and cleaning process of cotton textile manufacturing.
The Carding Process
The modern process of carding is a mechanical process in which the cotton fibres go through a series of processes to make them ready for later processing. This accomplishes the following:
- Separation and disentanglement of fibres
- Alignment of fibres
- Removal of short fibres
- Removal of impurities
- Blending of fibres
The carding machine is made up of a series of wire-wound cylinders that feature tiny teeth that run in opposite directions cut into them. The cotton fibres are passed through these series of rotating cylinders, with fibres passed from one cylinder to the other where the teeth get fine as the cotton progresses. Wire covered surfaces known as flats that are close to the main cylinder. As these cylinders act against one another, in conjunction with the flats, straightens and sligns the fibre. During this process the machine also further cleans the cotton fibre, removing more trash that wasn't caught in the earlier cleaning process.
The fibre is then condensed into something called a sliver, which is essentially a large rope of fibres, as it's passed through a trumpet or funnel. Finally, this sliver is coiled into a can for temporary storage before the next stage of the process. It sounds simple and efficient, but, as we'll find out in the next section, the process used to be far more labour intensive.
Carding by hand
Before carding machines existed, the process of carding was an exhausting manual process. One method required the use of hand carders, which are small paddles fitted with small cards (known as flick cards) that are used to flick the ends of a lock of fibre and remove strands for spinning off. A pair of hand carders are used to brush the fibre between them until they are more or less aligned in the same direction. The fibre is then peeled from the cards to create what’s known as a rolag. While animal fibres such as wool have traditionally been used to create rolags, today they can also be created by manufactured or plant-based fibres such as cotton.
Another method of hand carding is a drum carder, which is usually hand-cranked, but some drum carders powered by electric motors exist. These would work through the operation of two drums, or rollers, that are covered with card clothing. A smaller roller known as a licker-in takes in fibre from the intake tray and rolls it into the larger storage drum. A belt or chain drive connects the two rollers and, as the fibre is gently pulled from the licker-in, it straightens the fibres and they become wrapped between the pins of the card cloth on the storage drum. Once the card cloth is full the fibre is removed in batts (a flat mass of fibres) that is removed with a batt picker or doffer pin. You can see a drum carder in action in this video.
Luckily, we now have machines to carry out this process, otherwise the production of our cotton products would take an awful lot of labour and time. Small cottage industries in developing industries may still use hand methods, but it's more likely you'll find modern machinery carrying out the job.
The Combing Process
Combing is an optional extra stage in the process which improves the quality of the cotton but comes at the cost of the yarn. Cotton fibres are passed through fine metal teeth that slightly resemble those found on a comb used through your hair. One comb holds the fibre, while another comb is moved through so that the fibre is slowly transfered to the moving comb. This combing process removes the short fibres and arranges them into a flat bundle where all the fibres go in the same direction.
The result of combing cotton is that you get a stronger yarn, which ultimately means a stronger and more breathable fabric. It’s also a lot smoother and has a less hairy feel than non-combed cotton. You’ll also notice that the yarn has a higher lustre or shininess, as seen on the photo.
Combing cotton also helps improve the pilling (bobbling) resistance of a fabric as removing the short fibres means the resulting yarn will be less hairy and less likely to clump into bobbles on the fabric surface. If you want to learn how to avoid bobbling or pilling on your bed linen, then please take a look at our article on the topic.
Of course, all this comes with a trade-off. The combing process takes more time and generates more fibre wastage – up to 25% - which means that it will inevitably cost more. As a result, combed yarns are around 5% more expensive than carded yarns, which translates to a higher retail price for the final product.
After carding and, if carried out, the combing process are complete, the next stage in turning the fibre to yarn is spinning. This is quite an extensive topic, so we’ll cover that in the next article, which you can read by clicking here.
The full guide:
Read Part One - The Harvesting and Cleaning Process
Read Part Two - The Carding and Combing Process
Read Part Three - The Spinning Process
Read Part Four - The Weaving Process
Read Part Five - The Finishing Process
Read Part Six - The Product Makeup Process For Bedding & Towels